Implementing a robust foreign material control program is high on the priority list for meat processors globally, but misconceptions often delay getting the right inspection solutions in place. Can one inspection modality find it all? How does a traditional vision camera system differ from a hyperspectral camera? Which modality is best at finding low density materials? Do I need a multiple hurdle approach?
Alex Heater has answers. As the Technical Lead for Strategic Initiatives at PPO, she spends a lot of time working in different meat plant environments. She’s seen it all, fielded endless questions, and busted myths for meat processors big and small. We interviewed Alex to bring her knowledge to you.
Time to watch = 7 min 41 sec. Don’t have time? Skip straight to the highlights!
The myth of the “perfect” foreign material detection system (0:49):
“There’s no such thing as a perfect detection system. If it were perfect, it would detect everything and miss nothing. But in order to do that, it would have to reject everything, which isn’t great if you’re trying to make a profit or a product.” – Alex Heater, PPO’s Technical Lead for Strategic Initiatives
Size doesn’t (necessarily) matter (5:10):
“You can detect some materials down to one or two millimeters, but for any detection system out there, it really is going to depend on a multitude of factors. The background of what you’re running on, the type of foreign material, how it’s presented on the product, how it’s being presented to the detection system, even the environment can all impact how those technologies do on the detection sizes. For PPO specifically, with hyperspectral imaging if something has a really unique spectral signature or unique intensity compared to the background, we have a higher chance of being able to see those materials down to one or two millimeters.” Alex Heater, PPO’s Technical Lead for Strategic Initiatives
X-ray vs vision systems vs PPO (2:20):
“We actually did a study of PPO compared to an x-ray and a typical vision system. And in those results, we did a broader array of foreign materials, including some low density or less typical ones for those types of detection systems. PPO outperformed them by having better results across a broader range of foreign materials and, in many cases, better detection sizes than those.” – Alex Heater, PPO’s Technical Lead for Strategic Initiatives
Keep Learning with More Behind the Scenes Videos
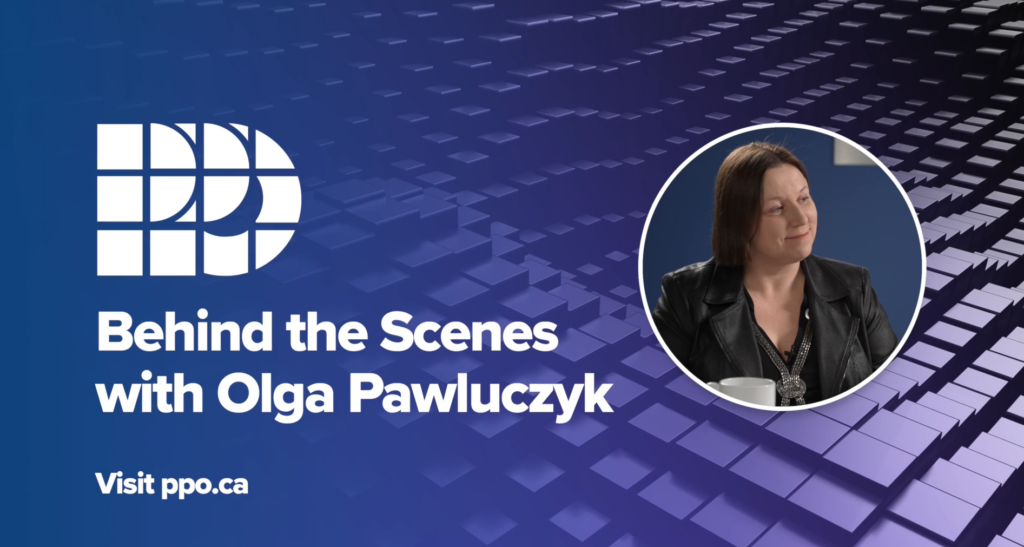
The Science Behind Hyperspectral Imaging
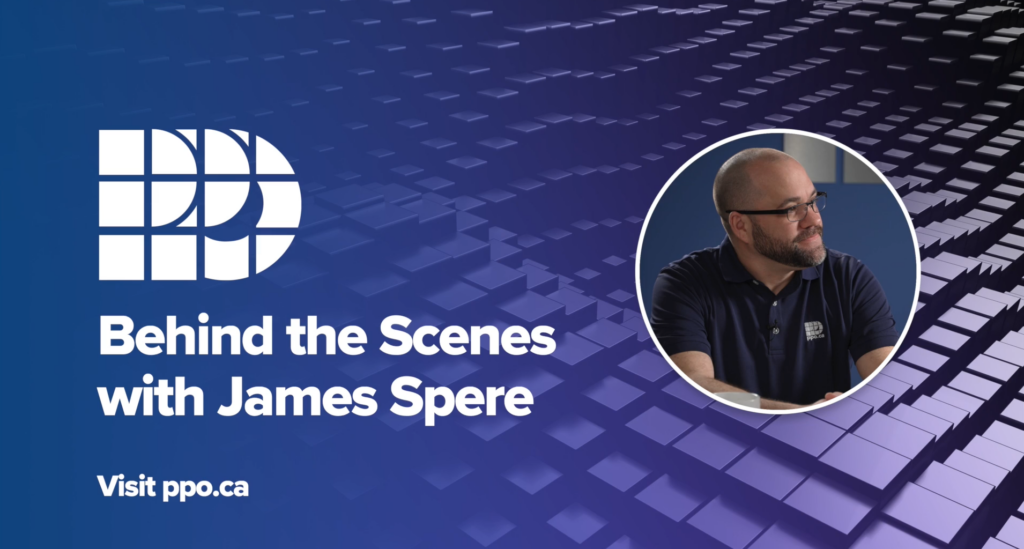
Artificial Intelligence Primer for Meat Processors
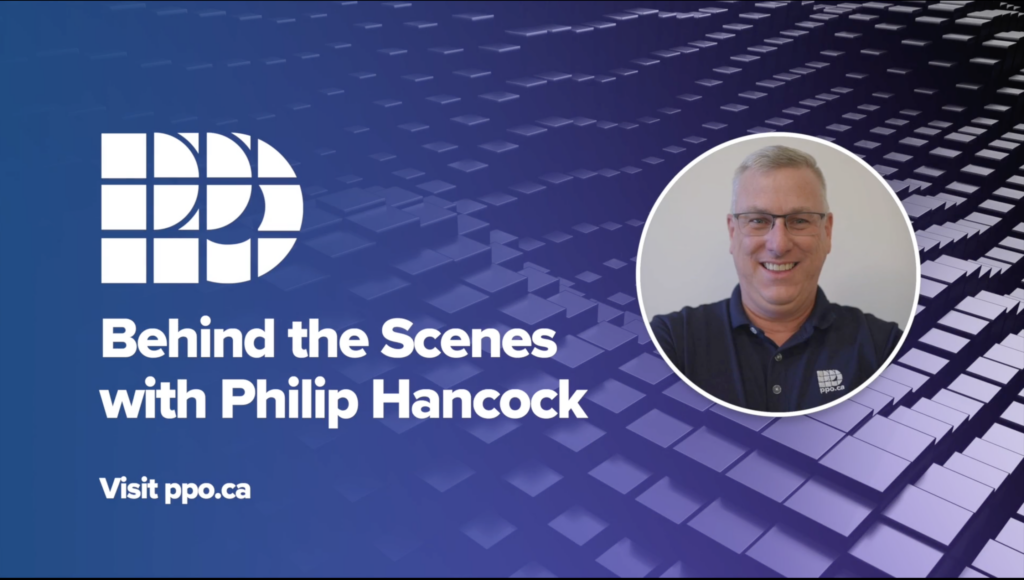
Foreign Material Detection in Action on the Front Lines of Meat Processing
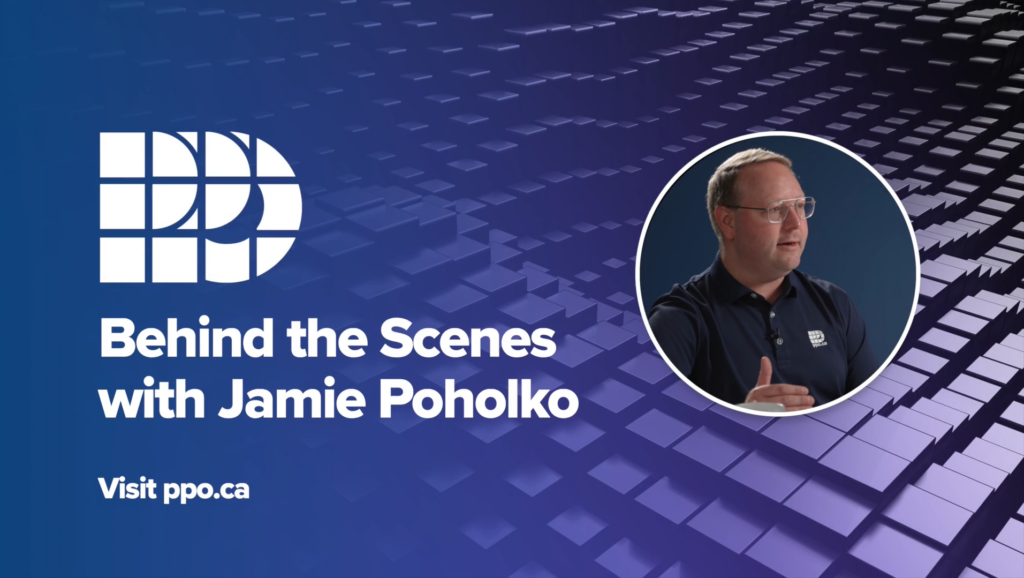
How to Work Smarter with Tech Companies to Maximize Impact
Read a Transcript of Alex’s Interview
Jump to the section of interest:
Heather Galt: Welcome to Behind the Scenes with PPO, a video series that looks behind the curtain at how meat processors are working with tech companies like PPO and why.
I’m Heather Galt, the Chief Customer Officer here at P&P Optica. And today, I’m joined by Alex Heater, the Technical Lead for Strategic Initiatives here at PPO.
Alex has been with us for about three years now and has worked in many different meat plant environments during that time. Welcome, Alex.
Alex Heater: Thank you.
Myth #1: A Single System Can Detect All Foreign Materials
HG: Today, we’re going to be doing some myth busting about foreign materials. And let’s start with a relatively common myth that there is one system that can rule them all and detect everything. Is that true?
AH: It’s not true. There’s no such thing as a perfect detection system. If it were perfect, it would detect everything and miss nothing. But in order to do that, it would have to reject everything, which isn’t great if you’re trying to make a profit.
HG: Or a product.
AH: Exactly.
It’s important to consider the problem that you’re trying to solve, and that can help tailor the solutions, but often the best case is to use a multi-hurdle approach, where you use multiple solutions to impact different factors of your problem.
An example of an industry that already does this is the medical field. You would never go and get a diagnosis using one test. You would use an array of different tests to get different results to be sure of the problem that you’re being diagnosed with.
Got it. So basically different modalities are being used to understand different parts of the problem or catch different things that might work together to get you the right answer.
HG: Exactly.
Myth #2: X-rays Are Sufficient for Foreign Material Detection
HG: Another misconception is that x-rays and a typical vision system would be sufficient to deal with the problem of foreign materials in a meat plant. What have you seen?
AH: In my experience, x-rays and visual systems aren’t the best at dealing with all of the foreign materials that are found in a plant. They have their specific advantages, so x-ray is really widely well known as being a great penetrative diagnosis tool for foreign materials. It can find foreign materials that are embedded in product.
Typical vision systems are good at high-contrast foreign materials. So anything that’s very high contrast, they can go down into great detail and find things very small.
Study Results of PPO vs X-ray vs a Typical Vision System
We actually did a study of PPO compared to an x-ray and a typical vision system. And in those results, we did a broader array of foreign materials, including some low density or less typical ones for those types of detection systems. PPO outperformed them by having better results across a broader range of foreign materials and, in many cases, better detection sizes than those.
HG: So, what would be an example of some of the low density materials that you were finding?
AH: So we’ve seen polyethylene, polypropylene, cardboard, wood, thin liners. Those are all four materials that PPO is good at detecting.
HG: And I think it’s pretty common in a meat plant, right?
AH: Oh, yes. I was at a customer site a little while ago, and we were running on ground pork. And within twenty-five minutes of turning the system on, we rejected quite a few foreign materials on product that had already been inspected by humans, including two pieces of four-millimeter shavings of polyethylene that looked to the human eye like fat.
HG: Wow. And something nobody really wants to bite into.
AH: No. Exactly.
Myth #3: Low density materials are hard to find
HG: Let’s talk a little more about those low density materials. Because I’ve heard this so many times in the industry: low density materials are just impossible to find. But it sounds like that’s not true.
AH: Yeah. It’s true in a sense of x-rays and typical vision systems. They have a hard time finding those types of foreign materials because where they are great is not on low density materials. Because PPO uses hyperspectral imaging, we’re able to use the spectral signatures and intensity of those foreign materials and differentiate them for the backgrounds.
HG: Got it. Okay.
Understanding Spectral Signatures
HG: I’m going to go off script for a minute. Talk to me a little bit about spectral signature. What does that mean? If I’m a meat processor, that’s something I’ve never heard before. What is it?
AH: Sure. It’s, for all intents and purposes, chemistry. When we use light, which is how we use our technology, anything in nature will absorb and reflect light based on its chemical composition. We can use the graphs that we get back from that reflectance to determine chemical composition and trends of certain components of foreign materials.
HG: Got it. Okay. So, you’re using light to understand chemistry and then figure out what belongs and what doesn’t, even if it looks the same color and looks kind of similar.
AH: Exactly.
HG: Okay. That’s awesome.
Myth #4: You Can’t Detect Tiny Foreign Materials
HG: You mentioned a little bit about tiny findings. – like little pieces of polypropylene shavings that nobody wants to bite into. And I’ve heard before, and I know most meat processors have heard, oh, we can find things down to 0.7 millimeters or 1 millimeter or 1/8 of an inch, or whatever metric they want to use. Is that true for all materials? And is it true for all modalities on all materials?
AH: You can detect some materials down to 1 or 2 millimeters, but for any detection system out there, it really is going to depend on a multitude of factors. The background of what you’re running on, the type of foreign material, how it’s presented on the product, how it’s being presented to the detection system, even the environment can all impact how those technologies do on the detection sizes.
For PPO specifically with hyperspectral imaging, if something has a really unique spectral signature or unique intensity compared to the background, we have a higher chance of being able to see those materials down to 1 or 2 millimeters.
HG: Got it. So really, no matter what technology you use, you kind of have to expect that one to two millimeters will be the optimal and not on every material.
AH: Yes.
HG: Got it. Okay.
Myth #5: Adopting Newer Technologies is Risky
HG: So, one last myth that I think we both probably want to dispel. And that is newer technologies, you know, especially in a meat plant or in another environment where there’s lots of risks and regulations, probably not a good idea to pursue newer technologies. What would you say to that?
AH: There’s always hesitancy when it comes to new technology in any industry.
It’s really kind of the mentality of “If it ain’t broke don’t fix it. Why should I introduce a new technology if the ones I have work?” But you should always be looking to improve upon what you have. It’s not really good to stay stagnant.
PPO is a proven technology. We’re in a multitude of different facilities in our customer sites providing value right now. We’re in RTE, primary and secondary facilities. We work on a range of backgrounds, including poultry, beef, and pork. We’re in many different applications and different environments.
As long as you know what the problem is that you’re trying to solve, you can mitigate anything that you can control. And then you consider technologies that are already being used and newer ones.
HG: So, basically, you’re thinking, and I agree, you always want to look at the whole range of applications and opportunities to fix the problem that you might have.
AH: Exactly.
HG: Awesome. Alright. Well, thank you very much for helping us dispel some of those myths today.
AH: Thank you.
HG: Don’t forget to check out the other videos in our Behind the Scenes series, including our interview with Jamie Poholko, where he talks about how meat processors and tech companies like PPO can work together better. See you next time!