With all the claims around food inspection modalities, it’s natural to question how hyperspectral imaging actually works. Help is here.
Olga Pawluczyk is the co-creator of PPO’s Smart Imaging System. In this quick 15-minute Behind the Scenes video, Olga clearly explains the science behind hyperspectral imaging. She also shares what differentiates this technology from modalities like x-ray and metal detectors when it comes to inspection of food products. Finally, she unpacks how to integrate hyperspectral imaging into your facility and start measuring ROI.
Don’t have time to watch? Skip to the highlights.
Hyperspectral Imaging System Video Highlights
Olga explains hyperspectral imaging in layman’s terms:
“Hyperspectral imaging is a method of imaging very similar to cameras. But, if you think about a human eye, we see only three colors in our eye. A camera will also see three colors. In the hyperspectral imaging systems that we deploy right now in food production, we see about five-to-six hundred colors. And that allows us to see chemistry of things that we inspect – in this case, food.”
Olga talks about the speed-sophistication tradeoff:
“What we’re seeing right now is most technologies, like x-rays and other vision systems, are less complex internally [than hyperspectral imaging]… basically, even though they might claim to have hyperspectral imaging, either they’re not using the same technology that we are or they’re not quite ready for the complexities and the challenges of a meat plant.”
Olga compares x-ray and metal detection to hyperspectral technology:
“I always think about it as I think about going to a doctor. You want your doctor to have multiple tools to diagnose whatever might be wrong with you…a break will be more visible with an x-ray, and a sprain will be better diagnosed with an ultrasound. It’s the same thing in industry…x-rays are fantastic at seeing things embedded in product. PPO sees things that x-rays will never see…low-density materials – like cardboard, wood, many plastics, many rubbers – that would be very difficult or impossible to see with x-rays.”
Keep Learning with More Behind the Scenes Videos
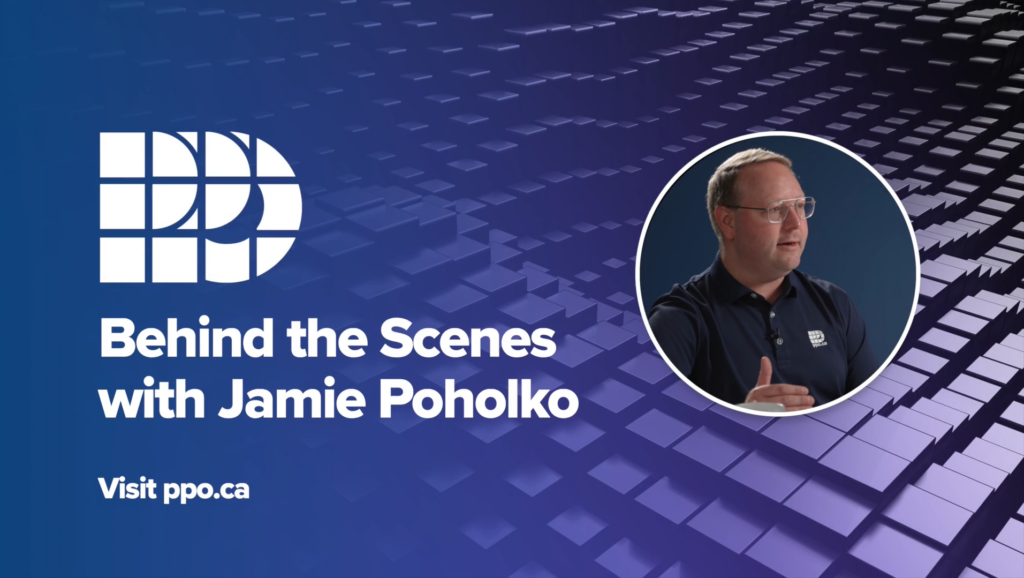
How to Work Smarter with Tech Companies to Maximize Impact
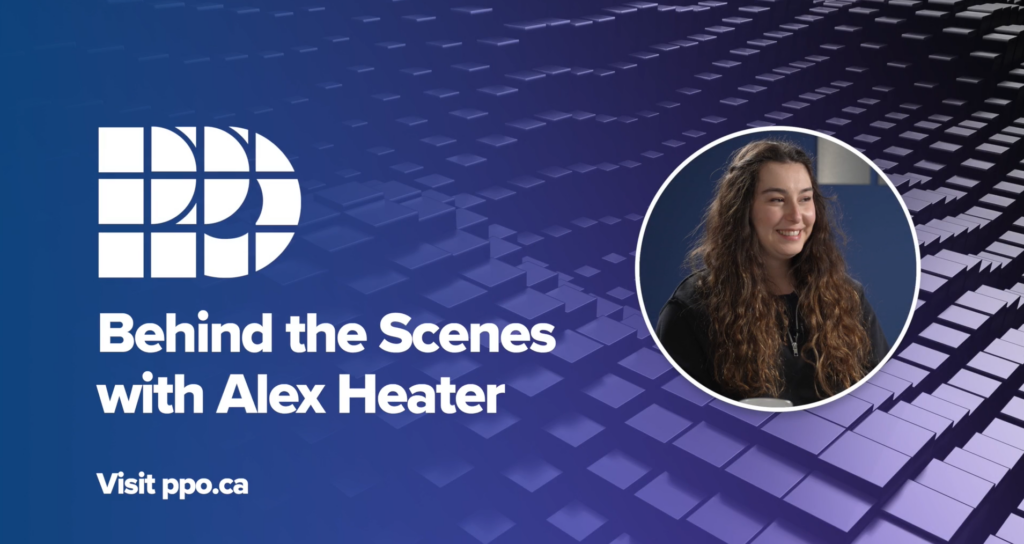
Dispel the Myths of Foreign Material Detection
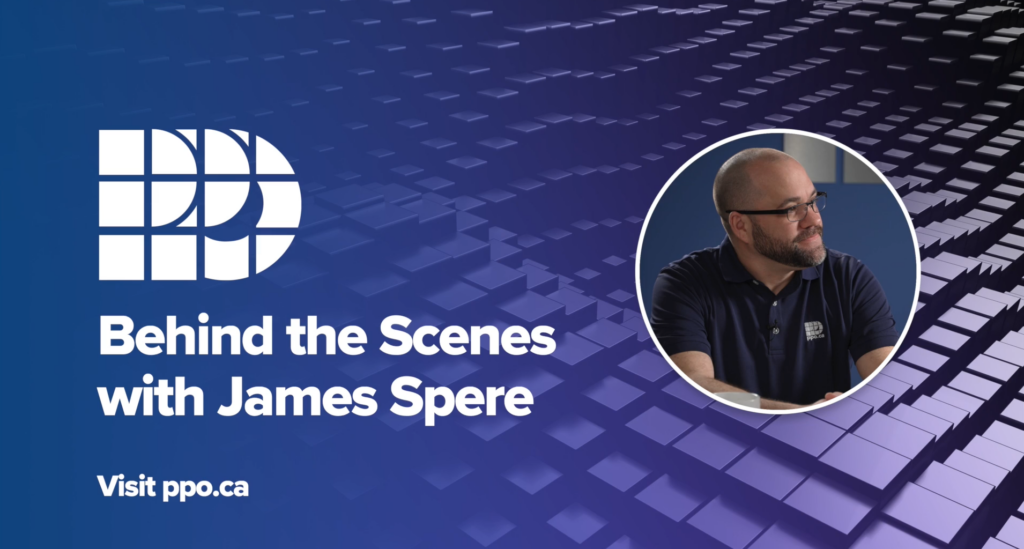
Artificial Intelligence Primer for Meat Processors
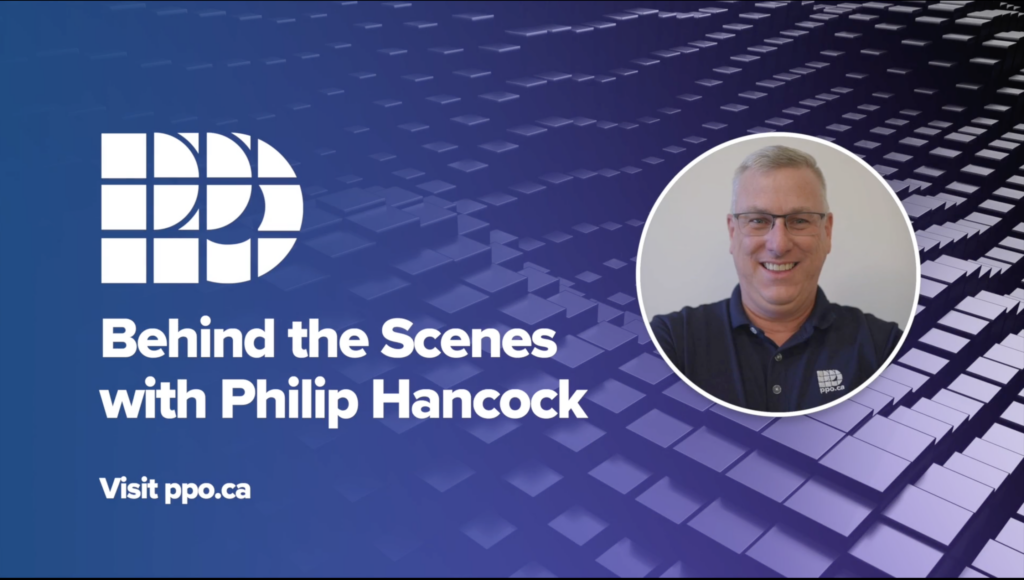
Incredible Foreign Material Examples From the Front Lines of Meat Processing
Read a Transcript of Olga’s Interview:
Jump to a section of interest:
- What is hyperspectral imaging?
- What makes hyperspectral imaging different?
- Why would a meat processor using other inspection modalities consider adding hyperspectral technology?
- Examples of where PPO is one of several modalities in a meat plant
- Ease of integrating a hyperspectral imaging system into an existing line
- Training a hyperspectral imaging system
- Measuring the ROI of hyperspectral technology
- Key questions to ask a hyperspectral imaging supplier
- The future of hyperspectral imaging – in the meat industry and beyond
Heather Galt: Welcome to Behind the Scenes with PPO, a video series that looks behind the curtain at how meat processors are working with tech companies like PPO and why.
I’m Heather Galt, the Chief Customer Officer here at P&P Optica. I’m here with Olga Pawluczyk, the CEO of PPO.
Olga has a background in medical imaging and has been the CEO here for over twenty years. She and her dad, Romek, developed the technology behind PPO’s system. So, there’s no one better to help us understand hyperspectral imaging and why it’s so darn good at solving challenges, like reducing foreign materials in meat processing.
Welcome, Olga.
Olga Pawluczyk: Hey, Heather.
What is hyperspectral imaging?
HG: Let’s start with a question that a newbie like me is going to ask. “What is hyperspectral imaging and why is it helpful in an environment like a meat plant?”
OP: So, hyperspectral imaging is a method of imaging very similar to cameras. But, if you think about a human eye, we see only three colors in our eye. A camera, typical camera like your iPhone, will see also three colors. In spectral imaging, we see hundreds of colors. So, in the systems that we deploy right now in food production, we see about five-to-six hundred collars. And that allows us to see chemistry of things that we inspect – in this case, food.
Awesome.
What makes hyperspectral imaging different?
HG: So, other companies in our industry and others claim they use hyperspectral imaging too. What makes us different? Why is PPO different?
OP: That’s a good question. And, look, hyperspectral imaging is used in many industries. But what we’re seeing right now is meat processing has a very different type of requirements that are needed for imaging. And right now, we seem to be the only hyperspectral imaging modality in meat processing.
What we need to do is, you know, when you think about a meat plant, not only do we have to image at the speed that meat plant runs, but we also have to survive the very critical cleaning process in in the meat industry.
So, building an optical system that can do things quickly, can calculate things quickly on a vast amount of data, and survives the day in, day out use of the meat industry is very difficult.
What we’re seeing right now is most technologies, like x-rays and other vision systems, are less complex internally and therefore can focus a little bit more on the engineering that can survive the rigors of the meat industry.
When though they might claim to have hyperspectral imaging, either they’re not using the same technology that we are or they’re not quite ready for the complexities and the challenges of a meat plant
That’s that’s what it looks like.
You know, again, if you look at the speed of the system, we have to look at conveyor belts going all the way to eighty-plus feet a minute. Very wide conveyor belts. We have to see down to about one-millimeter pixels and process all of that information.
I think what we’re seeing right now is with a lot of other technologies we’ll see just basic cameras, or maybe ten or so colors. Whereas that implementing of six hundred colors is complex, and we haven’t seen anybody in this space.
HG: Got it. Okay.
Why would a meat processor using other inspection modalities consider adding hyperspectral technology?
HG: If I’m a meat processor, and I already have an x-ray or metal detection system or maybe both, why would I consider using hyperspectral imaging too?
OP: Well, it’s a great question. And, you know, I always think about it as going to a doctor. You want your doctor to have multiple tools to diagnose whatever might be wrong with you. So if you break your ankle or you sprain your ankle, you might get an x-ray or you might get an ultrasound measurement.
Both of them are good at some things and not so great at other things. So a break will be more visible with an x-ray, and a sprain will be better diagnosed with an ultrasound. It’s the same thing in industry.
You know, x-rays are fantastic at seeing things that are embedded, that are dense, embedded in product.
We are a surface-only technique, but we see things that x-rays will never see. So things like things that float in water, so low density – like cardboard, wood, many plastics, many rubbers. They would be very difficult to see with x-rays or impossible to see with x-rays.
And metal detectors, I think they kind of mention already what they can see, and it’s they only see some metals.
So, we see a lot of customers using multiple modalities, including human inspectors, to really make their food production safer and better understood.
Examples of where PPO is one of several modalities in a meat plant
HG: Can you give me an example of what that’s meant in a plant? Are there any examples where PPO is one of a few different modalities being used?
OP: Oh, absolutely. We have multiple customers that have x-ray inspection at some point in the line, in the process, and will have a subsequent PPO system or maybe PPO goes before an X-ray.
And then close to packaging, final check, are there any metal bits that would be very unfortunate to end up at a consumer level? Metal detectors are also implemented.
Metal detectors and x-rays can penetrate through boxes and packaging, whereas we, as a surface-only method, can only see the surface. On the other hand, low-density materials, like rubbers and plastics tend to appear, you know, in the incoming product if it’s a secondary processor, or sometimes things like a glove or a hairnet falls into the process in a plant. So we’re there to inspect product as close to finished as possible as well.
Ease of integrating a hyperspectral imaging system into an existing line
HG: Okay, that’s awesome. How easy is it to integrate a hyperspectral imaging system like PPO into an existing line?
Well, it’s the same as any other equipment, you know. We take space and we take resources.
So, we typically work very closely with the customer. Their engineering team and our engineering team work together to make sure that there’s a sufficient amount of space, match the height of the belts, etc. Obviously, electrical, cooling, and so forth needs to be attached, but it’s no different than any other piece of equipment that needs to go into a process.
We work closely with the customer before the install happens. And then during install, we provide guidance, support, and sometimes labor as well.
HG: Is there anything special that has to be done to make a hyperspectral imaging system work in a plant?
OP: Not really. I mean, we have washdown in place…wiring, so we do need some water access. We do need to cool some of our cameras with relatively clean air, so there is typically some sort of cooler that’s required. And then electrical and Internet access. We do a lot of processing and data storage in the cloud, so Internet access is always beneficial as well.
Training a hyperspectral imaging system
HG: In one of our other videos, we talked to James Spere, PPO’s head of software and data, about training the system. Is that different than, say, an x-ray or a metal detector?
OP: I would say it’s more it’s more complex, but the same principles apply. We have to see the variability of the product. And, you know, the more deployments we have in multiple plants, the more of that we know internally as well.
But it’s very important to us to know more or less what’s happening in the plant. What’s the variability? What’s the temperature range? I would say that’s a little bit more complex than something like an x-ray.
But think about, you know, something like, the dogs we see sometimes in airports. If they only have to find one thing, obviously training for that would be very easy – find a treat. If they have to distinguish, let’s say three or four compounds, then training the dog is more complex.
The same translates to any computer vision or AI systems. The more complexity in the things you need to find, the more complex the training. The benefit is that our machines see multiple products across multiple factories. So the system that might be installed in Nebraska might learn from a system installed in Hawaii or something like that.
Measuring the ROI of hyperspectral technology
HG: Once we get to the point where the hyperspectral imaging system is installed in a plant – you buy the system, put it in, get it trained – how do customers that you’ve seen measure ROI from our system in particular?
OP: Well, you know, there’s this simple ROI. We eliminate the boring jobs that are extremely tedious to labor. But to me that’s, frankly, a little bit less exciting.
What we’re seeing is some customers can upgrade their product, for example, their SKUs. So instead of having a product that’s very low quality and might go into rendering, actually, it becomes now a consumable product that can go into further processing. Let’s say, meat hot dogs.
Because we not only find foreign materials, but also can measure fat lean, we can make a product much more consistent across the line, and that obviously reduces rework and issues with a final customer. So some of my favorite examples:
We had a customer that was about to lose one of their key customers. And we were able to prevent a lot of the foreign objects that were starting to make it to retail from actually happening. And therefore, they saved their customer relationship and actually increased the volume that they could produce for the customer.
The other story that I really enjoy is employee retention. So you get to work with technology. You don’t have to look at the product for eight hours in a day. Instead, you interact with the machine. That’s kind of interesting and does some, good rejection. So the work that the employee was doing was much more exciting and obviously beneficial to the company as well. And employees enjoy that, right? Like, when you have an interesting job, you’re more likely to stay somewhere.
HG: For sure. That’s one I would never have thought of. That’s really cool.
Key questions to ask a hyperspectral imaging supplier
HG: If I’m a meat processor, and I’m thinking about investing in a technology like hyperspectral imaging or another maybe newer to the market technology, what are some of the questions I should ask my supplier?
OP: Well, it’s very easy to give examples of the biggest success. So we see a half a millimeter for an object. The big question is how often do you see half a millimeter for an object? So I always laugh with our customers who know, for example, humans are excellent at finding an eyelash, but will miss the shovel going down.
Don’t worry about it. Not too many shovels make it through. But, you know, any diagnostic or detection system has a statistical probability of finding something.
So first of all, our system, we need to have something very well presented to it. So, you know, we have uniform product, and we don’t have anything hiding underneath it or something like that. So we flip the product, but you can imagine something stuck between two pieces.
In x-rays, again, density will be very important. So super-dense materials, x-rays can detect very small sizes. Less dense materials, they need to be larger.
Exact same thing happens in our technology.
How can I describe it? Think about a needle. And if you ever dropped a needle on the floor, which I have done, you know, in kindergarten, it’s way easier to find a needle when you have a nice white or dark surface. When you drop that needle on the carpet, the presentation of the needle itself makes finding it more difficult.
That applies to every single detection system, whether it’s MRI in medicine or hyperspectral imaging in a plant. It’s the same issue. You need contrast. You need to see the background differently than you see your object.
Ask about statistics. Ask about technology. Ask about stability. How do you calibrate the system? What is the support?
Dive deeper than just “this is the smallest thing we can find.” Because half of the time, they can’t find it.
And understanding, like you said, understanding the circumstances under which you can find it. So look: like a very nice piece of blue glove, we will find a tiny speck. But something that’s transparent, like tape, we need a larger chunk of it to kind of come out from the background. I don’t want to go into physics, but you need your photons. That’s what we’re measuring and they need to interact with the object that you’re looking at. If it’s super-transparent, super-thin, it’s next to impossible to detect any signal back.
HG: Right. Because there isn’t a signal coming back. Light passes through instead of coming back.
OP: Exactly.
HG: Got it.
The future of hyperspectral imaging – in the meat industry and beyond
HG: Okay. So, where do you see hyperspectral imaging going in the meat industry and elsewhere?
OP: Oh, it’s a fascinating thought process. You know, I think we’re barely scratching the surface right now. So we do very good for object detection or foreign material detection. Because we measure again, as I mentioned before, we measure chemical signatures. We measure interaction between molecules by measuring light reflecting off of these molecules.
I think my dream is that, instead of having, you know, derived nutritional facts on the cereal box, we will be able to measure the food that’s actually produced at a given time and packaged at a given time. Give you nutritional information, for example. Wouldn’t that be fun?
So, I can go to the grocery store and the package of hamburger that I buy, it’ll tell me exactly what the contents are of that box. I think type of fat, type of protein – I think that’s doable.
Do I think it’s coming, you know, in the next two months? I don’t think so.
But this is such important information for us as consumers, right? So, I think that’s what we could do.
I mean, it’s possible. This is measured in the lab all the time. We just have to accomplish the speed and really deal with the variability of food. You know, what goes on your pizza is way more complex than what goes into your iPhone. It varies so much more.
HG: Right. As you said before, there’s so much variability in the product and the plan.
OP: Exactly. Yeah.
HG: That’s awesome. Very cool. Thank you very much, Will. That’s really great.
OP: You’re welcome.
HG: What a great way to wrap up our conversation today. Don’t forget to check out the other videos in our behind the scenes series, including our interview with James Spere, the head of software and data that I mentioned before.
James pulls back the curtain on artificial intelligence, machine learning, and automation and meat processing. See you next time.