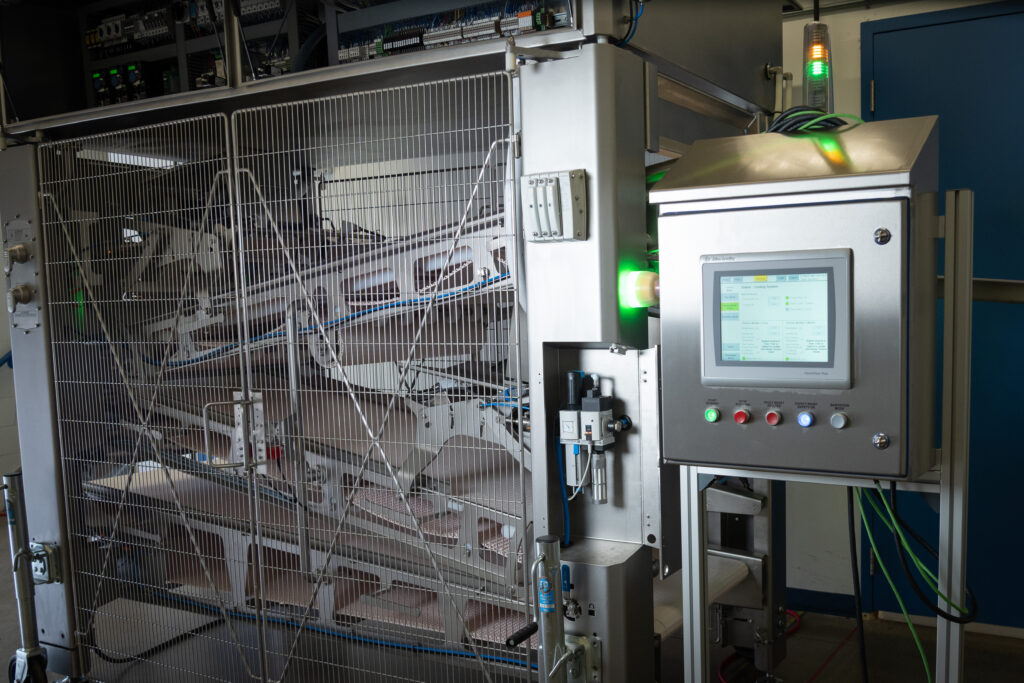
Every meat processing plant leader wants to have the right mix of automated inspection systems calibrated to capture foreign materials without over-inspecting and negatively impacting yields. Budgeting realities require making data-driven decisions before investing in any technology. With so many inspection technologies to choose from, it can be challenging to know where to invest for the greatest impact.
It makes sense to start by determining what type of foreign materials are causing problems in your plant. This ensures your chosen inspection technology is up to the task of detecting it.
If your foreign materials are mostly high-density materials, or metal, existing solutions like X-ray or metal detection may get the job done. If your plant is struggling with low-density materials – like plastic, wood and cardboard – or a wide variety of different materials, you may need to consider some of the newer technologies on the market, such as hyperspectral imaging. Implementing a multi-hurdle detection approach that relies on more than one technology is more expensive up front, but it can help to achieve zero foreign materials.
Once you’ve determined which inspection technology (or mix of technologies) will best detect your contaminants, you’re well on your way to optimizing your foreign material detection program. Before your organization makes any further investment, it makes sense to conduct a deeper analysis around the total return on investment (ROI) associated with the technology you’re considering. Here are four opportunities to realize ROI that should be on your radar when evaluating your options.
4 Measurable Impacts of an Automated Inspection System
1. Make the most of your human resources
A labor shortage continues to plague the meat processing industry. A recent FAIRR report shared that US job postings for meatpacking workers increased by 86% between 2017 and 2021. Predictions indicate the labor market will continue to be tight for the foreseeable future.
Results from the 2023 Manufacturing Survey published on foodprocessing.com revealed that 77% of respondents anticipate plant production to increase this year. When asked an open-ended question around their perceived “vital manufacturing issues” many commented on the problems of labor shortages and the quality of the workforce.
Automating visual inspection significantly reduces the need for human inspectors. For plants that do have sufficient staff to cover other critical operational functions, there’s an opportunity to save on headcount – to the tune of $50,000 to $75,000 per year, per employee. But with ongoing labor shortages, the bigger opportunity may be in cross-skilling or reskilling frontline inspectors to cover other roles:
- Boost operational flexibility. Training team members to perform multiple functions – from packaging to maintenance to logistics – gives you the freedom to shift workers in real time to meet the demands of the operation. Bonus: Introducing variety into an employee’s work life helps to mitigate boredom and improve employee retention.
- Breathe new life into a familiar job. Reskilling provides targeted training to help an employee shift into a new role. Automated inspection systems aren’t totally hands-off – they still require humans to keep them running properly. However, one team member can be trained to perform verification checks for multiple pieces of equipment. Building those specialized skills into an existing workforce is a popular approach. According to the 2023 Manufacturing Survey, over half of respondents said they are expanding in-house technical training to build the skills that automated systems demand.
- Improved engagement. When employees see chances to learn and grow with your company they’re 2.9x more likely to be engaged. Highly engaged employees are more motivated to do their best work and more likely to stay with your organization longer. Research from Gallup also shows that companies with engaged workforces have higher earnings per share (EPS)
Want to get a better handle on your potential labor savings with an automated inspection system? Our ROI calculator can help you see where to reallocate resources.
2. Minimize condemned product
Worldwide we waste 1.3 billion tons, or $2 trillion, of food every year. Condemned products in meat processing plants not only significantly contribute to this number, they erode your profits by reducing both yield and throughput.
Condemned product doesn’t have to be business as usual. For example, implementing PPO ‘s Smart Imaging System has helped customers reduce condemned product by up to 80%, with typical savings of between $500K and $1M per year. PPO combines hyperspectral imaging with advanced artificial intelligence (AI) and machine learning to measure product composition and identify foreign objects in real time, at line speed. Detecting quality issues early in the production process can significantly reduce condemned product and avoid costly rework.
Try out our ROI calculator to see how much you could save with an automated inspection system by reducing your condemned product.
3. Prevent Chargebacks
Despite best intentions and efforts, foreign materials slip through the cracks and end up in the hands of customers, the impact extends beyond the direct financial cost of the chargebacks – which often amount to tens or even hundreds of thousands of dollars. Chargebacks can also lead to damaged brand reputation and the potential loss of future business with the affected customer.
ROI in action
A harvest plant that serves food service and further processing was looking for an inspection solution to detect plastic, cardboard, and wood. They chose PPO’s Double-Sided Smart Imaging System to inspect whole muscle breasts and butterflies. This also led to them uncovering significant incidents of bone over the span of three weeks. They leveraged PPO Insights to trace the issue back to a maintenance issue further upstream. Identifying and addressing this issue reduced chargebacks by 40%.
Use our free ROI calculator to see how much you could save by counting on an automated inspection system to help prevent chargebacks.
4. Avoid Recalls
The average cost of a recall for food companies is estimated to be $10 million in direct costs. Any recall also has the potential to harm partner relationships, erode consumer trust, and even lead to costly litigation.
Foreign material was the top reason for USDA recalls in 2022, with one recall alone accounting for 148,000 pounds of frozen chicken breast due to suspected contamination with hard pieces of plastic. With the right mix of automated inspection systems in place, you can more easily detect foreign materials, including cardboard, plastic, wood, metal, rubber, glass, wood, steel and lead shot.
Sometimes contaminants are found further downstream, even after product has been inspected by your automated inspection system. Having access to your inspection data from PPO Insights (and other software tools) can protect your plant from recalls. You can combine the data with your own records to prove that the contaminant didn’t come from your plant.
Calculate your ROI
The four benefits outlined above are broadly associated with investing in an automated inspection system. The ROI you attribute to each of them will depend on specific nuances within your organization.
We’ve put together a calculator to help you customize the potential savings to your business. Don’t forget that detecting foreign materials early and often also offers positive ROI in the form of higher product quality and stronger customer experience.
Here’s one last point to consider: The best foreign materials detection solution addresses both measurement and decision making. It’s not just about seeing foreign materials, it’s about answering, “Is this actually a problem?” The ability to precisely answer this question is a huge competitive advantage.
PPO’s Smart Imaging System sees the chemistry of what it’s looking at and rapidly identifies what’s acceptable vs what needs to be rejected. The embedded AI and machine learning allows the solution to do this better and more precisely as time goes on.
If you’re ready to understand all the ways PPO’s proven and patented Smart Imaging System can significantly impact your bottom line, reach out.