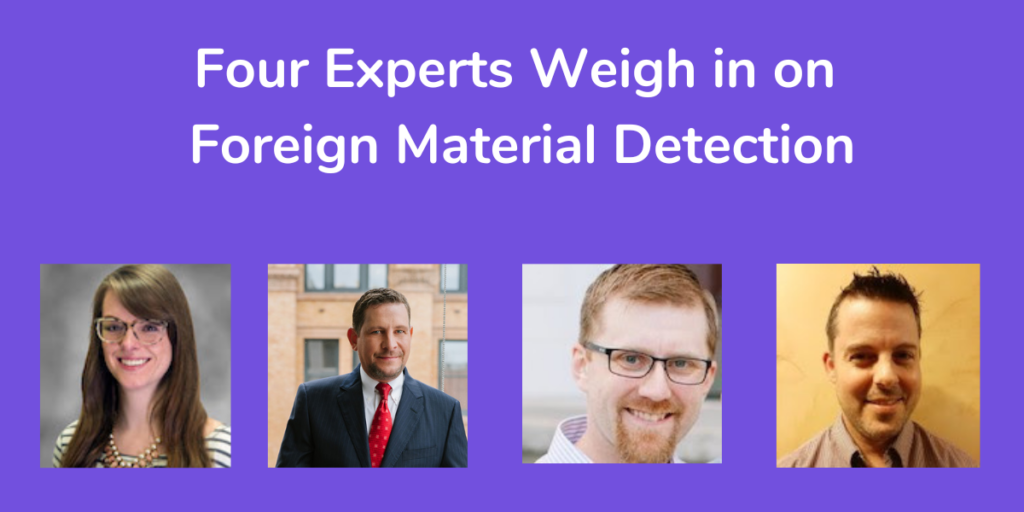
Foreign material contamination creates a multitude of issues for food processors and manufacturers. While the industry invests a huge amount of effort and resources into preventing and detecting foreign material in the food supply, as Shawn Stevens, founder of Food Industry Counsel, LLC, so aptly says, “Sometimes bad things do happen.”
Stevens was one of several experts who sat down with Maria Fontanazza, Editor-in-Chief at Food Safety Tech to discuss physical hazards in food processing. They were joined by Casey Gallimore, Director, Regulatory & Scientific Affairs at North American Meat Institute (NAMI); Chris Sawyer, Director, Continuous Improvement at Brakebush Brothers; and Scott Ruttgaizer, Product Manager at PPO.
While we may need to accept that foreign material incidents will occur in food processing for now, that doesn’t mean we can’t arm ourselves with expert answers to some big questions, including:
- How common are foreign material incidents and which way are they trending?
- What steps is the meat and poultry processing industry taking to address the problem?
- Are there resources and best practices that food processors can tap into as they work on their own foreign material prevention strategies?
- What are some real-life examples from the front lines of meat processing to get closer to a zero foreign material future?
These questions were top of mind for our panelists during their in-depth conversation. Since there was so much rich material covered in the session, we’ve recapped the highlights below. Watch for timecodes embedded in the post to check out specific moments.
How big is the foreign material problem?
The session started with Stevens digging into food recall data, and it revealed some interesting trends. There were relatively few recalls due to foreign materials in the early 2000s – under 20 each year. This was followed by a significant spike to over 50 a year between 2011 and 2012.
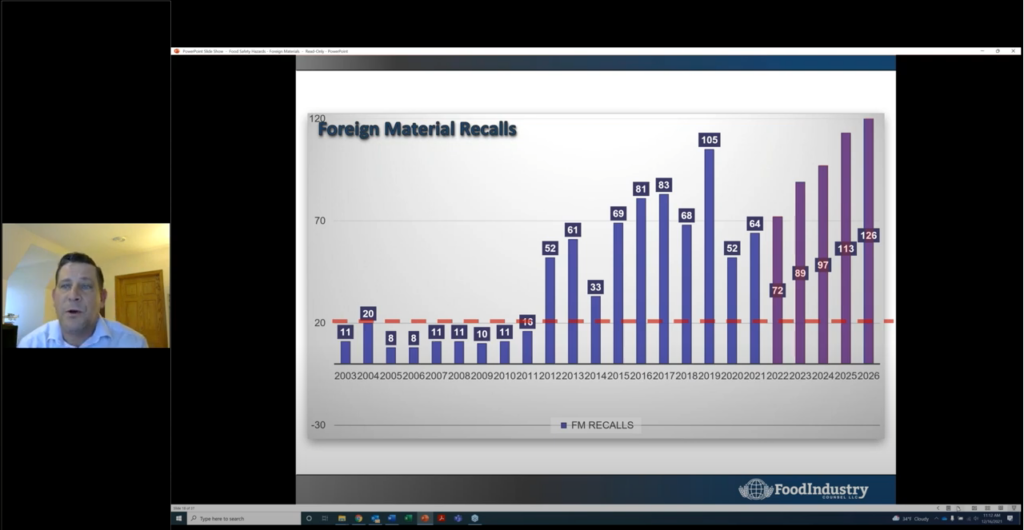
Watch Shawn Stevens unpack foreign material recalls in this clip.
While Stevens didn’t have a precise explanation for the jump in recalls, he shared they could be attributed to more companies investing in metal detection, coupled with the fact that 2011 was the same year that the Food Safety Modernization Act (FSMA) was written and signed into law.
He does expect to see an increasing number of recalls related to foreign materials moving forward, saying that “as more companies begin using technologies, such as X-ray, a lot of contamination that avoided detection previously will be detected.”
Casey Gallimore from NAMI has observed similar trends to Stevens. In fact, she shared that the meat and poultry industry hit a record high for the number of recalls in 2019, with foreign material responsible for 27%. She believes that additional factors influencing the increase in recalls include things like more regulatory focus and changes to policy initiatives.
Whatever the causes, the increase in foreign material contamination drove intensified efforts to focus attention on the issue. “At the end of the day, our industry recognized that there was just too much more [foreign] material,” said Gallimore. “And so, instead of focusing on why recalls increased, we could just focus on the main thing – which is to reduce the occurrence of foreign material in meat and poultry products.”
How is the meat and poultry industry tackling the foreign material issue?
Along with industry partners, stakeholders at NAMI sat down with their meat and poultry industry partners and distilled their priorities down to two areas. “Things break or things get lost,” Gallimore said. “So, we either need to break less things, or we need to manage things so they don’t get lost. And that was kind of easily broken into two projects.”
Gallimore concedes that these two projects won’t solve all foreign material contamination problems, but the working group felt confident they were an excellent start.
Project One: Equipment Design
Strategically equipment should result in fewer foreign material incidents. The same sanitary equipment design principles have long been in place for many years for the meat and poultry industry. So the working group updated and expanded them to cover all food safety hazards, with a specific focus on foreign material. The updated guide can be found in the Food Safety Equipment Design Principles Checklist & Glossary on the NAMI website.
“Designing equipment to reduce the likelihood that it’s going to break and cause more foreign material is a great effort,” said Gallimore. “But, at the end of the day, we also need to manage for when things do break, or to prevent things from getting lost. That was our second project.”
Project Two: Program Design
In a perfect world, equipment would never introduce foreign material. But in the real world, things will break and that needs to be properly managed. The program design project centered around creating a comprehensive Meat and Poultry Industry Foreign Material Manual to act as a reference and guide for leaders to use when creating their own internal programs. The manual is rooted in three main principles:
- Preventing foreign materials from occurring.
- Detecting foreign materials when they do occur.
- Responding appropriately to incidents.
During the session, Gallimore did a deep dive into the third principle of incident response.
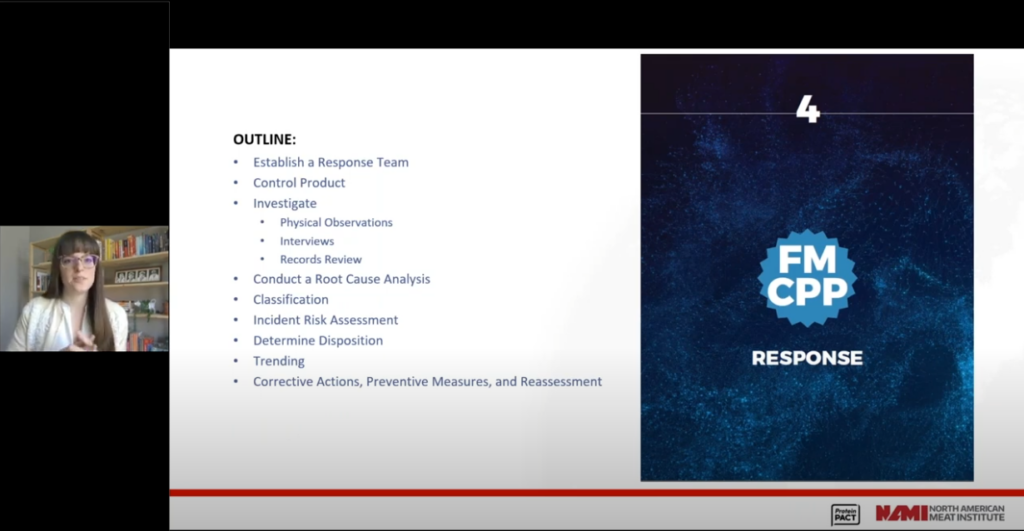
Watch Casey Gallimore dig into responding appropriately to foreign material events in this clip. You can also read about it starting on page 70 of the Foreign Material Manual.
The first step she encouraged was breaking apart what an incident is because that’s what helps you decide how to respond. There are essentially two types of incidentsoptions:
- An event occurs that could have resulted in foreign material ending up in the product. (Imagine an equipment failure, like a belt breaking, or a panicked employee reporting a missing glove.)
Gallimore’s biggest piece of quick-and-dirty advice? Make sure you’re actually missing something. If you are, then make sure you know specifically what’s missing before you go into a full-fledged response. “You would be amazed at the number of things that we had to “puzzle” back together over the years to confirm whether or not we were missing anything,” she said. This also helped them to clearly understand what they were looking for.
- A finding of foreign material in the product, either through inspection, a customer or (worst case) a consumer reporting it.
Tips for determining scope
One of the most challenging things about foreign material incidents is determining the scope. Gallimore says you need the right response team in place to do that. So, for example, if you suspect foreign material contamination is the result of mechanical failure, you definitely want maintenance to be involved. You’ll also want to include the person that works with the piece of equipment every day and those who were in the area where the incident may have happened.
“It doesn’t just need to be management personnel,” said Gallimore. “In fact, I find that it’s often way more valuable to have the boots-on-the-ground people than a management person.”
Gallimore suggested several proven strategies to try and identify what happened, including interviewing people that were in the area, conducting a thorough records review, documenting meticulously if it’s an external finding, and getting the foreign material back whenever possible.
“Having the physical form material is critically important in identifying,” she said. “I can’t tell you the number of times that we’ve looked at photos, even a photo next to a ruler, and something looks [one way]. Then we get the physical object and it’s something completely different than what we thought it was. And it’s much easier to run tests.”
When it comes to trying to fix a foreign material issue, there are three levels Gallimore outlined: Immediate corrective action, taking preventative measures, and reassessment.
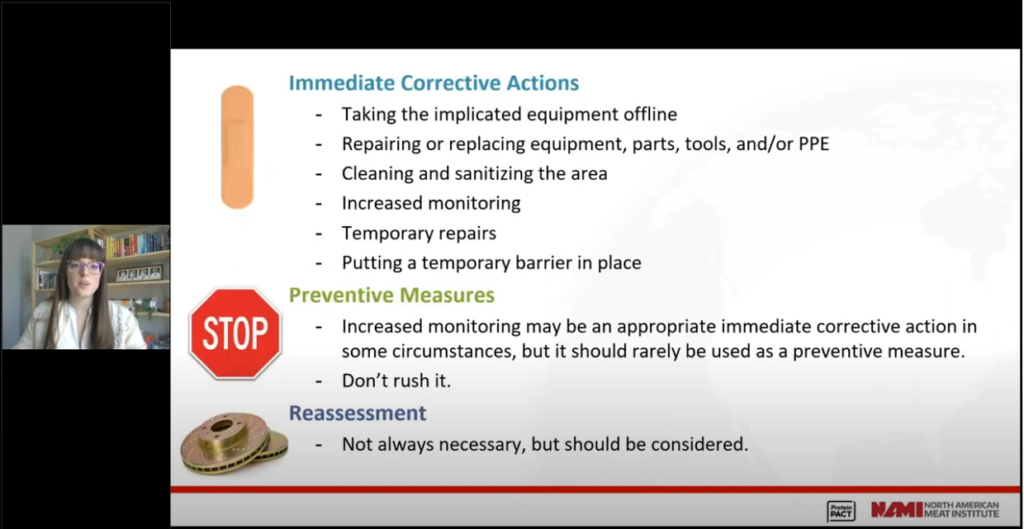
Watch Casey Gallimore walk through the three levels of addressing a foreign material issue in this clip.
Gallimore shared lots of great insights around programs, best practices, and links to helpful resources. She was followed by Chris Sawyer, Director of Continuous Improvement at Brakebush Brothers, who added to the conversation by giving us an up-close look into the realities of addressing foreign material on the front lines of value-added processing.
Get tips for foreign material prevention from a continuous improvement leader
Sawyer is clearly passionate about getting to a zero foreign material future and was generous enough to share a peek into projects and strategies leaders at Brakebush are pursuing to that end. (You can watch Chris’s entire talk here.)
Commit to a cultural shift
Sawyer said it’s not enough to have great detection technology in place and trust that it’s doing the job. You have to make eliminating foreign material a company-wide priority.
“If you don’t do that, you don’t build the culture around that goal,” said Sawyer. “You don’t put your money where your mouth is and you don’t truly invest in doing the right things. I think you’ll just continue to put bandaids on problems rather than actually heal the wound.”
Use the technology that’s going to work best for you
During his presentation, Sawyer discussed how all foreign material detection technologies offer benefits but also have shortcomings.
“You’re not going to find that silver bullet,” he said. “But I think back to my microbiology days and I think about when you talk about multi-hurdle technology and making the microbe face multiple hurdles. We can do the same thing here…leveraging multiple technologies either back to back or in different parts of your process where they’re going to be most impactful.”
Scott Ruttgaizer, Product Manager at P&P Optica, further drove this point home. Ruttgaizer knows that picking the right approach can be very challenging.
“Any approach is going to have trade-offs,” he said. “An x-ray machine is going to have very good detection for metal and stone and concrete and stuff like that. But it’s going to miss things like plastic and wood and cardboard that have less density gradient versus what you’re trying to detect. Vision inspection systems, spectrometers, can detect plastics and wood and all these things much much better. But there’s a trade off where it only does the surface. So you have to use whatever is at your disposal and mitigate these problems as best you can.”
Sawyer admits he was intrigued by the incremental ability of P&P Optica’s hyperspectral imaging technology to find foreign material previously undetectable by other technologies. “I remember reading through the literature and thinking ‘this is too good to be true,’” he said. “I can actually reliably find things like plastic and wood just by putting in this machine.”
While he had a healthy dose of skepticism, Sawyer was curious enough to investigate the technology further. Ultimately, Brakebush ended up putting PPO’s Smart Imaging System in as an offline process inspecting incoming raw material. While purchasing new technology to insert into their process was no small investment, Sawyer confirmed that they have the ROI to justify that it was worth trying something new.
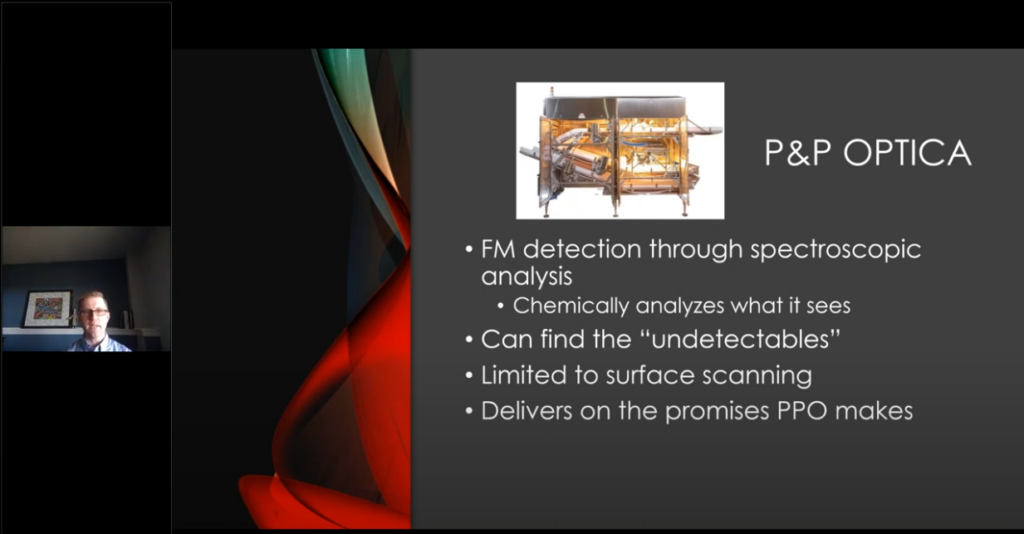
Watch Chris Sawyer talk about his experiences with implementing hyperspectral imaging.
“[With PPO], we routinely find previously undetectable materials, as small as two millimeters – really small pieces of plastic,” he said. “Even things like clear stretch wrap. It’s very difficult for us to find otherwise…it has delivered on and exceeded our expectations on the promises PPO was making.”
Don’t let perfect stand in the way of getting better
One final thought Sawyer shared about his journey was that progress is better than perfect, and you should never be afraid to fail.
“There is no perfection, but at least make progress from where you are today,” he said. “If there are gaps in your system, if there is an opportunity to upgrade technology and get more people involved, do that. Investigate what’s available to you that will give you a more reliable system for detecting and eliminating foreign material from your processes. Just keep moving forward.”
Just keep moving forward. This was the red thread running through each presentation in the session and it is sage advice for those who are committed to continuously work to eliminate foreign material from their processes.
You can access the entire session over here. And if you’d like to connect with one of our experts about how PPO can help you make progress on your foreign material detection, reach out. We’d love to chat.